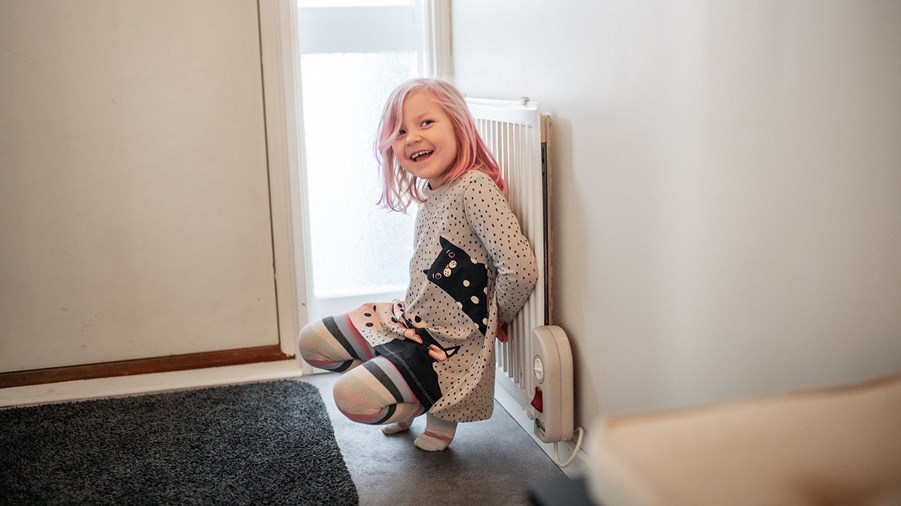
Solør Bioenergi is a leading supplier of renewable energy to buildings, with district heating generated using waste from forestry and sawmills. “We are clear – sawtimber that can store carbon for a century has no place in our furnaces. If we lose credibility on the sustainability front, we’ll soon be in trouble,” says Solør’s biofuel manager Hans M Moss.
It began with hazardous waste. The Norwegian wood product manufacturer Erik Lynne had been making weatherproof wooden poles since the 1960s when the 2002 ban on impregnation with CCA, a mix of chromium, copper and arsenic, was introduced. A large amount of treated wood was suddenly categorised as hazardous waste that needed to be rendered harmless. Lynne offered to burn the waste in a special furnace and recover the energy, eventually obtaining a permit to store the wood and build a cogeneration plant. The business was so successful that the CCA wood was soon not enough to keep up with demand, and so the company began also incinerating waste from forestry and the wider forest industry.
Sweden’s leading bio-energy supplier
The Norwegian company Solør Bioenergi has seen steady growth since early 2003 and now runs 70 district heating plants and 90 local heating plants in Norway and Sweden. At the start of the 2010s, the company identified Sweden as the world’s most attractive market for district heating. The first Swedish acquisition was a district heating plant in Charlottenberg, in the county of Värmland, in 2020, since when they have expanded east at a rapid pace. Today, Solør is Sweden’s leading supplier of renewable energy to homes, companies and industrial customers, with 235,000 daily users.
Also owns the district heating network
Solør still has three sites for the reception and incineration of hazardous wood waste, with the Trollhättan site specialising in used railway sleepers. They also own four pellet factories and a briquette factory, which together produce 140,000 tons of refined biofuel per year. But most of the fuel used for heat production is ‘virgin’ biofuel comprising – as the company’s biofuel manager Hans M Moss explains – treetops, branches, chips, shavings from sawmills and surplus roundwood purchased from local forest owners’ associations. Products from the forest industry account for the largest volumes.
“It’s a good symbiosis for all the parties. We are all dependent on each other,” says Moss, who also heads up the Norwegian division of Solør. “We have good relations with our suppliers.”
At the other end of the production chain, the company owns the entire infrastructure where it operates, i.e. the district heating network.
“We want to invest as much as possible in the value chain, but we have no plans to buy forest.”
District heat production using waste products
Up to 90 percent of the energy held in the biofuel is converted to heat. The figure is slightly lower for more moisture-heavy fuels such as bark, chips and other waste products from forestry. However, the furnaces are designed to take different kinds of fuel.
If damp fuel is added to a furnace, it goes through various zones – first a drying zone, then a combustion zone and finally an ash zone. The proportion of ash ranges between 0.5 and 2 percent, depending on the level of contaminated wood.
Hans Moss describes Solør’s district heat production as a zero-sum game. The plants emit no more carbon dioxide than is contained in the renewable fuel, while also allowing fossil fuel to stay in the ground.
“To maintain our credibility on the sustainability front, it is important that as much of the tree as possible is turned into sawn timber and wood products. Otherwise, we would soon be in trouble.
But the sawmills also need to get rid of their waste products,” says Moss.
“We’re also trying to keep transport to a minimum. There’s no point buying fuel in the south of Sweden and then driving it up to the north. So, we often enter into very local agreements with local suppliers.”
No burning of sawtimber
There are those who do not believe in this zero-sum game and claim that it is bad for the climate to burn biomass from the forest, whatever part of the forest production system it comes from.
“This is a misconception in environmental terms,” says Hans Moss. “And we’re very clear on this – sawtimber that can store carbon for a century has no place in our furnaces.”
Have you encountered any environmental criticism of your business?
“There’s been no direct confrontation. We are currently operating in countries where the forestry is a large and important industry, but we are observing a slightly different focus in certain parts of Europe.”
At the moment, the forests of Sweden and Norway are growing at a faster rate than they are being harvested, which means that the amount of biomass is rising. Hans Moss is optimistic about Solør’s business over the coming decades.
“And if in 20 years’ time, the view is that wood needs to be used for other things, other energy sources will no doubt be in play, like geothermal, for instance. That is bound to have been scaled up by then.”
Moss says that he is “alarmed as a woodsman and a forester” when people think that all oil can be replaced by carbon from the forest. That is not sustainable or possible and has never been on the table.
“The green transition is good, but you can’t put all your eggs in one basket.”
About Solør Bioenergi
- Founded in 2003 in the heavily forested district of Solør in eastern Norway, near the Swedish border with Värmland.
- Currently operates in 171 locations, primarily in Norway and Sweden (also in Poland).
- Runs 90 local heating plans and 70 district heating plants, the majority in Sweden.
- Owns 850 km of district heating pipes.
- Supplies district heating to 71 locations in Sweden.
- Supplies over 2.5 TWh energy in total.
- Has 5 biofuel factories (4 for pellets, 1 for briquettes).
- Has 3 sites for energy recovery from environmentally hazardous wood (creosote, CCA).